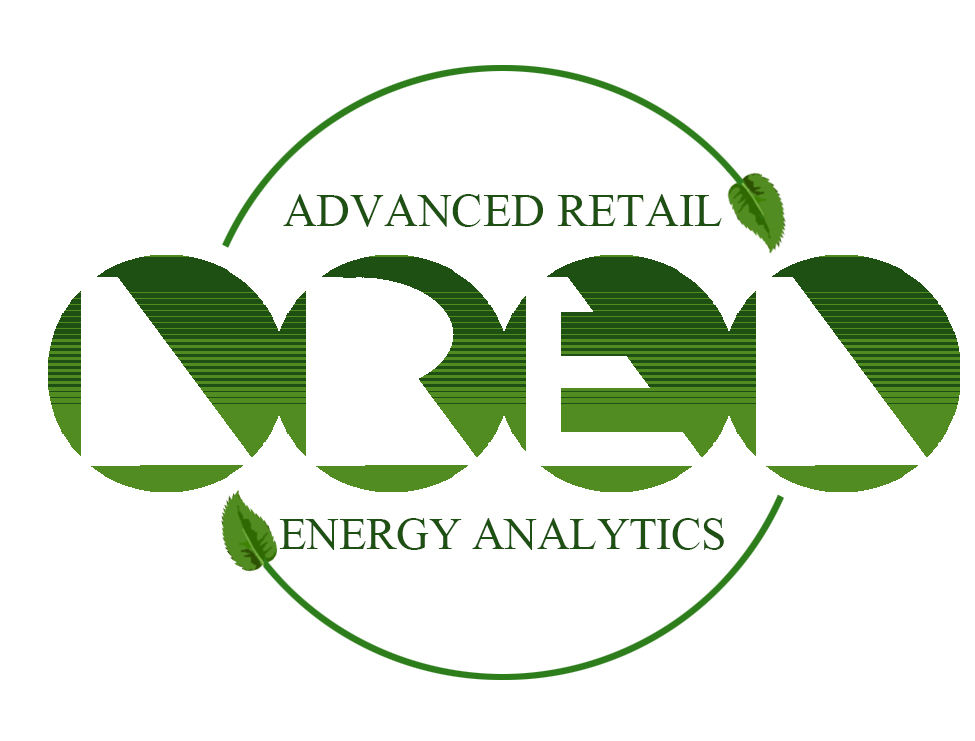
To: Executives Who Want to Improve Quality and Reduce Budgets
I have three questions to ask you:
-
What is your annual electric budget?
-
How many MEP[1] change orders do you pay on a new store?
-
How many truck rolls[2] are due to HVAC complaints in existing stores?
If you don’t like the answers or answered “I don’t know” to any of these questions my company CAN reduce your operating budgets by millions of dollars each year!
Most companies do not place a high prioritization on reducing their maintenance and energy costs since overall, it is a small percentage of the operating budget.
Even fewer companies have enough internal resources to investigate ways to reduce these budgets so they need to leverage outside vendors to perform these functions.
Hopefully I have grabbed your attention about all the financial savings and you are willing to read below the line!
AREA is a solution based consulting firm specializing in the design and construction industry that utilizes Kaizen[3] and other continuous improvement methods to simplify processes and improve quality to reduce Total Lifecycle (TLC) expenses. The most rewarding part of the process is knowing that you are also improving your company’s environment impact at the same time.
AREA started to evolve while I was attending conference’s such as RILA[4] and EEI[5]. My peers in the industry were curious of how I built a “Best in Class” energy management program at Abercrombie & Fitch. So, I started presenting at conferences and realized that these presentations, while effective at providing high level guidance to attendees, did not translate well into the execution phase since most companies lacked the internal resources with the proper expertise to successfully implement these initiatives.
AREA’s slogan is “Design with TLC in mind”. The first meaning of TLC is to design with Total Life Cycle to reduce operating and maintenance costs and the second meaning is to design with Tender, Love and Care about our environment. AREA calls this a win-win strategy for both the CFO and Sustainability and Environmental program. Developing a “Best in Class” energy program starts with analyzing every part of the store development process from leasing documents to preventative maintenance programs.
AREA wants to become a partner with your company; not just another vendor, and to be ingrained in the process as an external stakeholder who is viewed as a peer.
AREA looks forward to developing a long lasting and mutually beneficial relationship with your company.
[1] Mechanical, Electrical & Plumbing (MEP)
[2] Truck rolls are the amount of times a maintenance vendor comes to a store to fix an issue
[3] Kaizen is the Japanese work for “continuous improvement”. It refers to activities that continuously improve all functions and involve all employees from the CEO to the store employees.
[4] Retail Industry Leaders Association
[5] Edison Electric Institute